878 resultados para confinement, FRP, concrete, elliptical section, stress-strain behavior
Resumo:
This research paper presents the first results on the protein adsorption and release kinetics and in vitro biodegradability of cryogenically cured hydroxyapatite-gelatin based micro/macroporous scaffolds (CHAMPS). While the adsorption and release of bovine serum albumin (BSA) protein exhibits steady state behavior over an incubation period of up to 10 days, Fourier transform infrared (FT-IR) analysis importantly confirms the absence of any change in the secondary structure of BSA proteins due to interaction with the CHAMPS scaffold. The compression properties of the CHAMPS scaffold with interconnected porosity (pore size similar to 50-200 mm) is characterized by a non-linear stress-strain response with a strength close to 5 MPa and a maximum strain of up to 24%. The slow but systematic increase in weight loss over a period of 7 days as well as apatite layer formation indicates its good bioactivity. The extensive micro-computed tomography (micro-CT) analysis establishes cancellous bone-like highly interconnected and complex porous architecture of the CHAMPS scaffold. Importantly, the excellent adsorption (up to 50%) and release (up to 60% of adsorbed protein) of BSA has been uniquely attributed to the inherent porous microstructure of the CHAMPS scaffold. Overall, the present study provides an assessment of the interaction of protein with the gelatin-hydroxyapatite macroporous scaffold in vitro, as well as reporting for the first time the efficacy of such scaffolds to release 60% of BSA loaded onto the scaffold in vitro, which is significantly higher than earlier literature reports.
Resumo:
Free-standing Pt-aluminide (PtAl) bond coats exhibit a linear stress strain response under tensile loading and undergo brittle cleavage fracture at temperatures below the brittle-to-ductile transition temperature (BDTT). Above the BDTT, these coatings show yielding and fail in a ductile manner. In this paper, the various micromechanisms affecting the tensile fracture stress (FS) below the BDTT and yield strength (YS) above the BDTT in a PtAl bond coat have been ascertained and quantified at various temperatures. The micromechanisms have been identified by carrying out microtensile testing of stand-alone PtAl coating specimens containing different levels of Pt at temperatures between room temperature and 1100 degrees C and correlation of the corresponding fracture mechanisms with the deformation substructure in the coating. An important aspect of the influence of Pt on the tensile behavior, slip characteristics, FS/YS and BDTT in the PtAl coating has also been examined. The addition of Pt enhances the FS of the coating by Pt solid solution strengthening and imparts a concomitant increase in fracture toughness and yet causes a significant increase in the BDTT of the coating. Published by Elsevier Ltd. on behalf of Acta Materialia Inc.
Resumo:
Free-standing Pt-aluminide (PtAl) bond coat, when subjected to tensile testing at high temperatures (T >= 900 degrees C), exhibits significant decrease in strength and increase in ductility during deformation at strains exceeding that corresponding to the ultimate tensile strength (UTS), i.e., in the post-UTS regime. The stress-strain curve is also marked by serrations in this regime. Electron back scattered diffraction (EBSD) and transmission electron microscopy (TEM) studies suggest dynamic recovery and recrystallization (DRR) as the mechanisms for the observed tensile behavior in the coating. Activation energy values suggest vacancy diffusion assists DRR. The fine recrystallized grains formed after deformation had a strong < 110 > texture. (c) 2014 Elsevier B.V. All rights reserved.
Resumo:
The distribution of stress-strain near a crack tip in a rubber sheet is investigated by employing the constitutive relation given by Gao (1997). It is shown that the crack tip field is composed of two shrinking sectors and one expanding sector. The stress state near the crack tip is in uniaxial tension. The analytical solutions are obtained for both expanding and shrinking sectors.
Resumo:
This paper deals with the quantitative prediction of the volume fraction of martensitic transformation in a austenitic steel that undergoes impact with high strain rate. The coupling relations between strain, stress, strain rate, transformation rate and transformed fraction were derived from the OTC model and modified Bodner-Partom equations, where the impact process was considered as an adiabatic and no entropy-increased process (pressure less than or equal to 20GPa). The one-dimensional results were found to model and predict various experimental results obtained on 304 stainless steel under impact with high strain rate.
Resumo:
Spherical nanoindentation tests were performed on Zr41.2Ti13.8Cu12.5Ni10Be22.5 bulk metallic glass and pile-ups were observed around the indenter. A new modified expanding cavity model was developed to characterize the indentation deformation behavior of strain-hardening and pressure-dependent materials. By using this model, the representative stress-strain response of this bulk metallic glass to hardness and indentation in the elastic-plastic regime were obtained taking into consideration the effect of pile-up.
Resumo:
With a newly developed Material Failure Process Analysis code (MFPA(2D)), influence of hetero geneity on fracture processes and strength characterization of brittle disorder materials such as rock or concrete is numerically studied under uniaxial compression and tension conditions. It is found th at, due to the heterogeneity of the disordered material, relatively more diffused micro-fractures appear in the early stage of loading. Different from homogeneous materials such as glass, macro-crack nucleation starts well before the peak stress is reached and the crack propagation and coalescence can be traced, which can be taken as a precursory to predict the macro-fracture of the material. The presence of residual strength in the post-peak region and the resemblance in the stress-strain curves between tension and compression are significant results and are found to be dependent on the heterogeneity of the specimens. Examples showing the tentative applications of MFPA(2D) in modeling failure of composite materials and rock or civil engineering problem are also given in this paper.
Resumo:
Based on the microscopic observations and measurements, the mechanical behavior of the surface-nanocrystallized Al-alloy material at microscale is investigated experimentally and theoretically. In the experimental research, the compressive stress-strain curves and the hardness depth curves are measured. In the theoretical simulation, based on the material microstructure characteristics and the experimental features of the compression and indentation, the microstructure cell models are developed and the strain gradient plasticity theory is adopted. The material compressive stress-strain curves and the hardness depth curves-are predicted and simulated. Through comparison of the experimental results with the simulation results, the material and model parameters are determined.
Fracture Mechanisms And Size Effects Of Brittle Metallic Foams: In Situ Compression Tests Inside Sem
Resumo:
In situ compressive tests on specially designed small samples made from brittle metallic foams were accomplished in a loading device equipped in the scanning electron microscopy (SEM). Each of the small samples comprises only several cells in the effective test zone (ETZ), with one major cell in the middle. In such a system one can not only obtain sequential collapse-process images of a single cell and its cell walls with high resolution, but also correlate the detailed failure behaviour of the cell walls with the stress-strain response, therefore reveal the mechanisms of energy absorption in the mesoscopic scale. Meanwhile, the stress-strain behaviour is quite different from that of bulk foams in dimensions of enough large, indicating a strong size effect. According to the in situ observations, four failure modes in the cell-wall level were summarized, and these modes account for the mesoscopic mechanisms of energy absorption. Paralleled compression tests on bulk samples were also carried out, and it is found that both fracturing of a single cell and developing of fracture bands are defect-directed or weakness-directed processes. The mechanical properties of the brittle aluminum foams obtained from the present tests agree well with the size effect model for ductile cellular solids proposed by Onck et al. (C) 2008 Elsevier Ltd. All rights reserved.
Resumo:
We present a model in this paper for predicting the inverse Hall-Petch phenomenon in nanocrystalline (NC) materials which are assumed to consist of two phases: grain phase of spherical or spheroidal shapes and grain boundary phase. The deformation of the grain phase has an elasto-viscoplastic behavior, which includes dislocation glide mechanism, Coble creep and Nabarro-Herring creep. However the deformation of grain boundary phase is assumed to be the mechanism of grain boundary diffusion. A Hill self-consistent method is used to describe the behavior of nanocrystalline pure copper subjected to uniaxial tension. Finally, the effects of grain size and its distribution, grain shape and strain rate on the yield strength and stress-strain curve of the pure copper are investigated. The obtained results are compared with relevant experimental data in the literature.
Resumo:
Pile-up around indenter is usually observed during instrumented indentation tests on bulk metallic glass. Neglecting the pile-up effect may lead to errors in evaluating hardness, Young's modulus, stress-strain response, etc. Finite element analysis was employed to implement numerical simulation of spherical indentation tests on bulk metallic glass. A new model was proposed to describe the pile-up effect. By using this new model, the contact radius and hardness of Zr41.2Ti13.8Cu12.5Ni10Be22.5 bulk metallic glass were obtained under several different indenter loads with pile-up, and the results agree well with the data generated by numerical simulation.
Resumo:
The close form solutions of deflections and curvatures for a film-substrate composite structure with the presence of gradient stress are derived. With the definition of more precise kinematic assumption, the effect of axial loading due to residual gradient stress is incorporated in the governing equation. The curvature of film-substrate with the presence of gradient stress is shown to be nonuniform when the axial loading is nonzero. When the axial loading is zero, the curvature expressions of some structures derived in this paper recover the previous ones which assume the uniform curvature. Because residual gradient stress results in both moment and axial loading inside the film-substrate composite structure, measuring both the deflection and curvature is proposed as a safe way to uniquely determine the residual stress state inside a film-substrate composite structure with the presence of gradient stress.
Resumo:
Results of tensile and compression tests on a short-glass-fiber-reinforced thermotropic liquid crystalline polymer are presented. The effect of strain rate on the compression stress-strain characteristics has been investigated over a wide range of strain rates epsilon between 10(-4) and 350 s-1. The low-strain-rate tests were conducted using a screw-driven universal tensile tester, while the high-strain-rate tests were carried out using the split Hopkinson pressure bar technique. The compression modulus was shown to vary with log10 (epsilon) in a bilinear manner. The compression modulus is insensitive to strain rate in the low-strain-rate regime (epsilon = 10(-4) - 10(-2) s-1), but it increases more rapidly with epsilon at higher epsilon. The compression strength changes linearly with log10 (epsilon) over the entire strain-rate range. The fracture surfaces were examined by scanning electron microscopy.
Resumo:
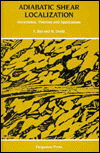
Table of Contents
1 | Introduction | 1 |
1.1 | What is an Adiabatic Shear Band? | 1 |
1.2 | The Importance of Adiabatic Shear Bands | 6 |
1.3 | Where Adiabatic Shear Bands Occur | 10 |
1.4 | Historical Aspects of Shear Bands | 11 |
1.5 | Adiabatic Shear Bands and Fracture Maps | 14 |
1.6 | Scope of the Book | 20 |
2 | Characteristic Aspects of Adiabatic Shear Bands | 24 |
2.1 | General Features | 24 |
2.2 | Deformed Bands | 27 |
2.3 | Transformed Bands | 28 |
2.4 | Variables Relevant to Adiabatic Shear Banding | 35 |
2.5 | Adiabatic Shear Bands in Non-Metals | 44 |
3 | Fracture and Damage Related to Adiabatic Shear Bands | 54 |
3.1 | Adiabatic Shear Band Induced Fracture | 54 |
3.2 | Microscopic Damage in Adiabatic Shear Bands | 57 |
3.3 | Metallurgical Implications | 69 |
3.4 | Effects of Stress State | 73 |
4 | Testing Methods | 76 |
4.1 | General Requirements and Remarks | 76 |
4.2 | Dynamic Torsion Tests | 80 |
4.3 | Dynamic Compression Tests | 91 |
4.4 | Contained Cylinder Tests | 95 |
4.5 | Transient Measurements | 98 |
5 | Constitutive Equations | 104 |
5.1 | Effect of Strain Rate on Stress-Strain Behaviour | 104 |
5.2 | Strain-Rate History Effects | 110 |
5.3 | Effect of Temperature on Stress-Strain Behaviour | 114 |
5.4 | Constitutive Equations for Non-Metals | 124 |
6 | Occurrence of Adiabatic Shear Bands | 125 |
6.1 | Empirical Criteria | 125 |
6.2 | One-Dimensional Equations and Linear Instability Analysis | 134 |
6.3 | Localization Analysis | 140 |
6.4 | Experimental Verification | 146 |
7 | Formation and Evolution of Shear Bands | 155 |
7.1 | Post-Instability Phenomena | 156 |
7.2 | Scaling and Approximations | 162 |
7.3 | Wave Trapping and Viscous Dissipation | 167 |
7.4 | The Intermediate Stage and the Formation of Adiabatic Shear Bands | 171 |
7.5 | Late Stage Behaviour and Post-Mortem Morphology | 179 |
7.6 | Adiabatic Shear Bands in Multi-Dimensional Stress States | 187 |
8 | Numerical Studies of Adiabatic Shear Bands | 194 |
8.1 | Objects, Problems and Techniques Involved in Numerical Simulations | 194 |
8.2 | One-Dimensional Simulation of Adiabatic Shear Banding | 199 |
8.3 | Simulation with Adaptive Finite Element Methods | 213 |
8.4 | Adiabatic Shear Bands in the Plane Strain Stress State | 218 |
9 | Selected Topics in Impact Dynamics | 229 |
9.1 | Planar Impact | 230 |
9.2 | Fragmentation | 237 |
9.3 | Penetration | 244 |
9.4 | Erosion | 255 |
9.5 | Ignition of Explosives | 261 |
9.6 | Explosive Welding | 268 |
10 | Selected Topics in Metalworking | 273 |
10.1 | Classification of Processes | 273 |
10.2 | Upsetting | 276 |
10.3 | Metalcutting | 286 |
10.4 | Blanking | 293 |
Appendices | 297 | |
A | Quick Reference | 298 |
B | Specific Heat and Thermal Conductivity | 301 |
C | Thermal Softening and Related Temperature Dependence | 312 |
D | Materials Showing Adiabatic Shear Bands | 335 |
E | Specification of Selected Materials Showing Adiabatic Shear Bands | 341 |
F | Conversion Factors | 357 |
References | 358 | |
Author Index | 369 | |
Subject Index | 375 |
Resumo:
Due to their high specific strength and low density, magnesium and magnesium-based alloys have gained great technological importance in recent years. However, their underlying hexagonal crystal structure furnishes Mg and its alloys with a complex mechanical behavior because of their comparably smaller number of energetically favorable slip systems. Besides the commonly studied slip mechanism, another way to accomplish general deformation is through the additional mechanism of deformation-induced twinning. The main aim of this thesis research is to develop an efficient continuum model to understand and ultimately predict the material response resulting from the interaction between these two mechanisms.
The constitutive model we present is based on variational constitutive updates of plastic slips and twin volume fractions and accounts for the related lattice reorientation mechanisms. The model is applied to single- and polycrystalline pure magnesium. We outline the finite-deformation plasticity model combining basal, pyramidal, and prismatic dislocation activity as well as a convexification based approach for deformation twinning. A comparison with experimental data from single-crystal tension-compression experiments validates the model and serves for parameter identification. The extension to polycrystals via both Taylor-type modeling and finite element simulations shows a characteristic stress-strain response that agrees well with experimental observations for polycrystalline magnesium. The presented continuum model does not aim to represent the full details of individual twin-dislocation interactions, yet it is sufficiently efficient to allow for finite element simulations while qualitatively capturing the underlying microstructural deformation mechanisms.