129 resultados para Stress strain tests
em Chinese Academy of Sciences Institutional Repositories Grid Portal
Resumo:
Based on the 'average stress in the matrix' concept of Mori and Tanaka (:Mori, T., Tanaka, K., 1973. Average stress in matrix and average elastic energy of materials with misfitting inclusion. Acta Metall. 21, 571-580) a micromechanical model is presented for the prediction of the elastic fields in coated inclusion composites with imperfect interfaces. The solutions of the effective elastic moduli for this kind of composite are also obtained. In two kinds of composites with coated particulates and fibers, respectively, the interface imperfections are takes to the assumption that the interface displacement discontinues are linearly related to interface tractions like a spring layer of vanishing thickness. The resulting effective shear modulus for each material and the stress fields in the composite are presented under a transverse shear loading situation.
Resumo:
Applying the scaling relationships developed recently for conical indentation in elastic-plastic solids with work-hardening, we examine the question of whether stress-strain relationships of such solids can be uniquely determined by matching the calculated loading and unloading curves with that measured experimentally. We show that there can be multiple stress-strain curves for a given set of loading and unloading curves. Consequently, stress-strain relationships may not be uniquely determined from loading and unloading curves alone using a conical or pyramidal indenter.
Resumo:
Plastic stress-strain fields of two types of steel specimens loaded to large deformations are studied. Computational results demonstrate that, owing to the fact that the hardening exponent of the material varies as strain enlarges and the blunting of the crack tip, the well known HRR stress field in the plane strain model can only hold for the stage of a small plastic strain. Plastic dilatancy is shown to have substantial effects on strain distributions and blunting. To justify the constitutive equations used for analysis and to check the precision of computations, the load-deflection of a three-point bend beam and the load-elongation of an axisymmetric bar notched by a V-shaped cut were tested and recorded. The computed curves are in good accordance with experimental data.
Fracture Mechanisms And Size Effects Of Brittle Metallic Foams: In Situ Compression Tests Inside Sem
Resumo:
In situ compressive tests on specially designed small samples made from brittle metallic foams were accomplished in a loading device equipped in the scanning electron microscopy (SEM). Each of the small samples comprises only several cells in the effective test zone (ETZ), with one major cell in the middle. In such a system one can not only obtain sequential collapse-process images of a single cell and its cell walls with high resolution, but also correlate the detailed failure behaviour of the cell walls with the stress-strain response, therefore reveal the mechanisms of energy absorption in the mesoscopic scale. Meanwhile, the stress-strain behaviour is quite different from that of bulk foams in dimensions of enough large, indicating a strong size effect. According to the in situ observations, four failure modes in the cell-wall level were summarized, and these modes account for the mesoscopic mechanisms of energy absorption. Paralleled compression tests on bulk samples were also carried out, and it is found that both fracturing of a single cell and developing of fracture bands are defect-directed or weakness-directed processes. The mechanical properties of the brittle aluminum foams obtained from the present tests agree well with the size effect model for ductile cellular solids proposed by Onck et al. (C) 2008 Elsevier Ltd. All rights reserved.
Resumo:
The distribution of stress-strain near a crack tip in a rubber sheet is investigated by employing the constitutive relation given by Gao (1997). It is shown that the crack tip field is composed of two shrinking sectors and one expanding sector. The stress state near the crack tip is in uniaxial tension. The analytical solutions are obtained for both expanding and shrinking sectors.
Resumo:
This paper deals with the quantitative prediction of the volume fraction of martensitic transformation in a austenitic steel that undergoes impact with high strain rate. The coupling relations between strain, stress, strain rate, transformation rate and transformed fraction were derived from the OTC model and modified Bodner-Partom equations, where the impact process was considered as an adiabatic and no entropy-increased process (pressure less than or equal to 20GPa). The one-dimensional results were found to model and predict various experimental results obtained on 304 stainless steel under impact with high strain rate.
Resumo:
This paper first presents a stochastic structural model to describe the random geometrical features of rock and soil aggregates. The stochastic structural model uses mixture ratio, rock size and rock shape to construct the microstructures of aggregates,and introduces two types of structural elements (block element and jointed element) and three types of material elements (rock element, soil element, and weaker jointed element)for this microstructure. Then, continuum-based discrete element method is used to study the deformation and failure mechanism of rock and soil aggregate through a series of loading tests. It is found that the stress-strain curve of rock and soil aggregates is nonlinear, and the failure is usually initialized from weaker jointed elements. Finally, some factors such as mixture ratio, rock size and rock shape are studied in detail. The numerical results are in good agreement with in situ test. Therefore, current model is effective for simulating the mechanical behaviors of rock and soil aggregates.
Resumo:
Spherical nanoindentation tests were performed on Zr41.2Ti13.8Cu12.5Ni10Be22.5 bulk metallic glass and pile-ups were observed around the indenter. A new modified expanding cavity model was developed to characterize the indentation deformation behavior of strain-hardening and pressure-dependent materials. By using this model, the representative stress-strain response of this bulk metallic glass to hardness and indentation in the elastic-plastic regime were obtained taking into consideration the effect of pile-up.
Resumo:
Pile-up around indenter is usually observed during instrumented indentation tests on bulk metallic glass. Neglecting the pile-up effect may lead to errors in evaluating hardness, Young's modulus, stress-strain response, etc. Finite element analysis was employed to implement numerical simulation of spherical indentation tests on bulk metallic glass. A new model was proposed to describe the pile-up effect. By using this new model, the contact radius and hardness of Zr41.2Ti13.8Cu12.5Ni10Be22.5 bulk metallic glass were obtained under several different indenter loads with pile-up, and the results agree well with the data generated by numerical simulation.
Resumo:
In the present research, microstructure of a kind of limnetic shell (Hyriopsis cumingii) is observed and measured by using the scanning electron microscopy, and mechanical behavior experiments of the shell nacre are carried out by using bending and tensile tests. The dependence of mechanical properties of the shell nacre on its microstructure is analyzed by using a modified shear-lag model, and the overall stress-strain relation is obtained. The experimental results reveal that the mechanical properties of shell nacre strongly depend on the water contents of the limnetic shell. Dry nacre shows a brittle behavior, whereas wetting nacre displays a strong ductility. Compared to the tensile test, the bending test overestimates the strength and underestimates the Young's modulus. The modified shear-lag model can characterize the deformation features of nacre effectively.
Resumo:
The plane strain asymptotic fields for cracks terminating at the interface between elastic and pressure-sensitive dilatant material are investigated in this paper. Applying the stress-strain relation for the pressure-sensitive dilatant material, we have obtained an exact asymptotic solution for the plane strain tip fields for two types of cracks, one of which lies in the pressure-sensitive dilatant material and the other in the elastic material and their tips touch both the bimaterial interface. In cases, numerical results show that the singularity and the angular variations of the fields obtained depend on the material hardening exponent n, the pressure sensitivity parameter mu and geometrical parameter lambda.
Resumo:
The close form solutions of deflections and curvatures for a film-substrate composite structure with the presence of gradient stress are derived. With the definition of more precise kinematic assumption, the effect of axial loading due to residual gradient stress is incorporated in the governing equation. The curvature of film-substrate with the presence of gradient stress is shown to be nonuniform when the axial loading is nonzero. When the axial loading is zero, the curvature expressions of some structures derived in this paper recover the previous ones which assume the uniform curvature. Because residual gradient stress results in both moment and axial loading inside the film-substrate composite structure, measuring both the deflection and curvature is proposed as a safe way to uniquely determine the residual stress state inside a film-substrate composite structure with the presence of gradient stress.
Resumo:
Results of tensile and compression tests on a short-glass-fiber-reinforced thermotropic liquid crystalline polymer are presented. The effect of strain rate on the compression stress-strain characteristics has been investigated over a wide range of strain rates epsilon between 10(-4) and 350 s-1. The low-strain-rate tests were conducted using a screw-driven universal tensile tester, while the high-strain-rate tests were carried out using the split Hopkinson pressure bar technique. The compression modulus was shown to vary with log10 (epsilon) in a bilinear manner. The compression modulus is insensitive to strain rate in the low-strain-rate regime (epsilon = 10(-4) - 10(-2) s-1), but it increases more rapidly with epsilon at higher epsilon. The compression strength changes linearly with log10 (epsilon) over the entire strain-rate range. The fracture surfaces were examined by scanning electron microscopy.
Resumo:
The present paper aims to develop a robust spherical indentation-based method to extract material plastic properties. For this purpose, a new consideration of-piling-up effect is incorporated into the expanding cavity model; an extensive numerical study on the similarity Solution has also been performed. As a consequence, two semi-theoretical relations between the indentation response and material plastic properties are derived, with which plastic properties of materials can be identified from a single instrumented spherical indentation curve, the advantage being that this approach no longer needs estimations of contact radius with given elastic modulus. Moreover, the inconvenience in using multiple indenters with different tip angles can be avoided. Comprehensive sensitivity analyses show that the present algorithm is reliable. Also, by experimental verification performed oil three typical materials, good agreement of the material properties between those obtained from the reverse algorithm and experimental data is obtained.
Resumo:
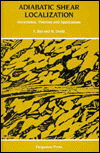
Table of Contents
1 | Introduction | 1 |
1.1 | What is an Adiabatic Shear Band? | 1 |
1.2 | The Importance of Adiabatic Shear Bands | 6 |
1.3 | Where Adiabatic Shear Bands Occur | 10 |
1.4 | Historical Aspects of Shear Bands | 11 |
1.5 | Adiabatic Shear Bands and Fracture Maps | 14 |
1.6 | Scope of the Book | 20 |
2 | Characteristic Aspects of Adiabatic Shear Bands | 24 |
2.1 | General Features | 24 |
2.2 | Deformed Bands | 27 |
2.3 | Transformed Bands | 28 |
2.4 | Variables Relevant to Adiabatic Shear Banding | 35 |
2.5 | Adiabatic Shear Bands in Non-Metals | 44 |
3 | Fracture and Damage Related to Adiabatic Shear Bands | 54 |
3.1 | Adiabatic Shear Band Induced Fracture | 54 |
3.2 | Microscopic Damage in Adiabatic Shear Bands | 57 |
3.3 | Metallurgical Implications | 69 |
3.4 | Effects of Stress State | 73 |
4 | Testing Methods | 76 |
4.1 | General Requirements and Remarks | 76 |
4.2 | Dynamic Torsion Tests | 80 |
4.3 | Dynamic Compression Tests | 91 |
4.4 | Contained Cylinder Tests | 95 |
4.5 | Transient Measurements | 98 |
5 | Constitutive Equations | 104 |
5.1 | Effect of Strain Rate on Stress-Strain Behaviour | 104 |
5.2 | Strain-Rate History Effects | 110 |
5.3 | Effect of Temperature on Stress-Strain Behaviour | 114 |
5.4 | Constitutive Equations for Non-Metals | 124 |
6 | Occurrence of Adiabatic Shear Bands | 125 |
6.1 | Empirical Criteria | 125 |
6.2 | One-Dimensional Equations and Linear Instability Analysis | 134 |
6.3 | Localization Analysis | 140 |
6.4 | Experimental Verification | 146 |
7 | Formation and Evolution of Shear Bands | 155 |
7.1 | Post-Instability Phenomena | 156 |
7.2 | Scaling and Approximations | 162 |
7.3 | Wave Trapping and Viscous Dissipation | 167 |
7.4 | The Intermediate Stage and the Formation of Adiabatic Shear Bands | 171 |
7.5 | Late Stage Behaviour and Post-Mortem Morphology | 179 |
7.6 | Adiabatic Shear Bands in Multi-Dimensional Stress States | 187 |
8 | Numerical Studies of Adiabatic Shear Bands | 194 |
8.1 | Objects, Problems and Techniques Involved in Numerical Simulations | 194 |
8.2 | One-Dimensional Simulation of Adiabatic Shear Banding | 199 |
8.3 | Simulation with Adaptive Finite Element Methods | 213 |
8.4 | Adiabatic Shear Bands in the Plane Strain Stress State | 218 |
9 | Selected Topics in Impact Dynamics | 229 |
9.1 | Planar Impact | 230 |
9.2 | Fragmentation | 237 |
9.3 | Penetration | 244 |
9.4 | Erosion | 255 |
9.5 | Ignition of Explosives | 261 |
9.6 | Explosive Welding | 268 |
10 | Selected Topics in Metalworking | 273 |
10.1 | Classification of Processes | 273 |
10.2 | Upsetting | 276 |
10.3 | Metalcutting | 286 |
10.4 | Blanking | 293 |
Appendices | 297 | |
A | Quick Reference | 298 |
B | Specific Heat and Thermal Conductivity | 301 |
C | Thermal Softening and Related Temperature Dependence | 312 |
D | Materials Showing Adiabatic Shear Bands | 335 |
E | Specification of Selected Materials Showing Adiabatic Shear Bands | 341 |
F | Conversion Factors | 357 |
References | 358 | |
Author Index | 369 | |
Subject Index | 375 |