80 resultados para shear-stress
Resumo:
In this paper, an improved plate impact experimental technique is presented for studying dynamic fracture mechanism of materials, under the conditions that the impacting loading is provided by a single pulse and the loading time is in the sub-microsecond range. The impacting tests are carried out on the pressure-shear gas gun. The loading rate achieved is dK/dt similar to 10(8) MPa m(1/2) s(-1). With the elimination of influence of the specimen boundary, the plane strain state of a semi-infinite crack in an infinite elastic plate is used to simulate the deformation fields of crack tip. The single pulses are obtained by using the "momentum trap" technique. Therefore, the one-time actions of the single pulse are achieved by eradicating the stress waves reflected from the specimen boundary or diffracted from the crack surfaces. In the current study, some important phenomena have been observed. The special loading of the single pulse can bring about material damage around crack tip, and affect the material behavior, such as kinking and branching of the crack propagation. Failure mode transitions from mode I to mode II crack are observed under asymmetrical impact conditions. The mechanisms of the dynamic crack propagation are consistent with the damage failure model.
Resumo:
A three-phase piezoelectric cylinder model is proposed and an exact solution is obtained for the model under a farfield antiplane mechanical load and a far-field inplane electrical load. The three-phase model can serve as a fiber/interphase layer/matrix model, in terms of which a lot of interesting mechanical and electrical coupling phenomena induced by the interphase layer are revealed. It is found that much more serious stress and electrical field concentrations occur in the model with the interphase layer than those without any interphase layer. The three-phase model can also serve as a fiber/matrix/composite model, in terms of which a generalized self-consistent approach is developed for predicting the effective electroelastic moduli of piezoelectric composites. Numerical examples are given and discussed in detail.
Resumo:
Lateral stress of LY-12 alummium alloy under plate impact shock loading was measured. Based on the measured data, the Hugoniot relation and shear strength were obtained. The result has demonstrated that the shear strenath of the tested material increases remarkably with the increasing longitudinal stress. This means that the assumption of constant shear strength usually adopted in shock stress calculation is not suitable for the present material.
Resumo:
The torsional impact response of a penny-shaped crack in an unbounded transversely isotropic solid is considered. The shear moduli are assumed to be functionally graded such that the mathematics is tractable. Laplace transform and Hankel transform are used to reduce the problem to solving a Fredholm integral equation. The crack tip stress fields are obtained. Investigated are the influence of material nonhomogeneity and orthotropy on the dynamic stress intensity factor. The peak value of the dynamic stress intensity factor can be suppressed by increasing the shear moduli's gradient and/or increasing the shear modulus in a direction perpendicular to the crack surface.
Resumo:
formula for the thickness of a shear band formed in saturated soils under a simple shear or a combined stress state has been proposed. It is shown that the shear band thickness is dependent on the pore pressure properties of the material and the dilatancy rate, but is independent of the details of the combined stress state. This is in accordance with some separate experimental observations.
Resumo:
Investigations made by the authors and collaborators into the microstructural aspects of adiabatic shear localization are critically reviewed. The materials analyzed are low-carbon steels, 304 stainless steel, monocrystalline Fe-Ni-Cr, Ti and its alloys, Al-Li alloys, Zircaloy, copper, and Al/SiCp composites. The principal findings are the following: (a) there is a strain-rate-dependent critical strain for the development of shear bands; (b) deformed bands and white-etching bands correspond to different stages of deformation; (c) different slip activities occur in different stages of band development; (d) grain refinement and amorphization occur in shear bands; (e) loss of stress-carrying capability is more closely associated with microdefects rather than with localization of strain; (f) both crystalline rotation and slip play important roles; and (g) band development and band structures are material dependent. Additionally, avenues for new research directions are suggested.
Resumo:
Adopting Yoshizawa's two-scale expansion technique, the fluctuating field is expanded around the isotropic field. The renormalization group method is applied for calculating the covariance of the fluctuating field at the lower order expansion. A nonlinear Reynolds stress model is derived and the turbulent constants inside are evaluated analytically. Compared with the two-scale direct interaction approximation analysis for turbulent shear flows proposed by Yoshizawa, the calculation is much more simple. The analytical model presented here is close to the Speziale model, which is widely applied in the numerical simulations for the complex turbulent flows.
Resumo:
An infinite elastic solid containing a doubly periodic parallelogrammic array of cylindrical inclusions under longitudinal shear is studied. A rigorous and effective analytical method for exact solution is developed by using Eshelby's equivalent inclusion concept integrated with the new results from the doubly quasi-periodic Riemann boundary value problems. Numerical results show the dependence of the stress concentrations in such heterogeneous materials on the periodic microstructure parameters. The overall longitudinal shear modulus of composites with periodic distributed fibers is also studied. Several problems of practical importance, such as those of doubly periodic holes or rigid inclusions, singly periodic inclusions and single inclusion, are solved or resolved as special cases. The present method can provide benchmark results for other numerical and approximate methods. (C) 2003 Elsevier Ltd. All rights reserved.
Resumo:
The dynamic stress intensity factor histories for a half plane crack in an otherwise unbounded elastic body are analyzed. The crack is subjected to a traction distribution consisting of two pairs of suddenly-applied shear point loads, at a distance L away from the crack tip. The exact expression for the combined mode stress intensity factors as the function of time and position along the crack edge is obtained. The method of solution is based on the direct application of integral transforms together with the Wiener-Hopf technique and the Cagniard-de Hoop method, which were previously believed to be inappropriate. Some features of solutions are discussed and the results are displayed in several figures.
Resumo:
Examined in this work is the anti-plane stress and strain near a crack in a material that softens beyond the elastic peak and unloads on a linear path through the initial state. The discontinuity in the constitutive relation is carried into the analysis such that one portion of the local solution is elliptic in character and the other hyperbolic. Material elements in one region may cross over to another as the loading is increased. Local unloading can thus prevail. Presented are the inhomogeneous character of the asymptotic stress and strain in the elliptic and hyperbolic region, in addition to the region in which the material elements had experienced unloading. No one single stress or strain coefficient would be adequate for describing crack instability.
Resumo:
EXPERIMENTS carried out using a split Hopkinson torsional bar have shown that only one shear band develops in specimens of hot rolled steel which break during testing. We observed, however, that in specimens which were not deformed to failure, several fine shear bands appeared. We believe that these formed during the loading cycle before the appearance of the final shear band and were not due to the effect of unloading. So we developed a numerical model to study the evolution of shear banding from several finite amplitude disturbances (FADs) in both temperature and strain rate. This numerical model reveals the detailed processes by which the FADs evolve into a fully developed shear band and suggests that beyond instability, the so-called shear banding process consists of two stages: inhomogeneous shearing and true shear-banding. The latter is characterized by the collapse of the stress and an abrupt increase of the local shear strain rate.
Resumo:
A theoretical description of thermo-plastic instability in simple shear is presented in a system of equations describing plastic deformation, the first law of thermodynamics and Fourier's heat transfer rule. Both mechanical and thermodynamical parameters influence instability and it is shown that two different modes of instability may exist. One of them is dominated by thermal softening and has a characteristic time and length, connected to each other by thermal diffusion.A criterion combining thermal softening, current stress, density, specific heat, work-hardening, thermal conductivity and current strain rate is obtained and practical implications are discussed.
Resumo:
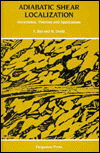
Table of Contents
1 | Introduction | 1 |
1.1 | What is an Adiabatic Shear Band? | 1 |
1.2 | The Importance of Adiabatic Shear Bands | 6 |
1.3 | Where Adiabatic Shear Bands Occur | 10 |
1.4 | Historical Aspects of Shear Bands | 11 |
1.5 | Adiabatic Shear Bands and Fracture Maps | 14 |
1.6 | Scope of the Book | 20 |
2 | Characteristic Aspects of Adiabatic Shear Bands | 24 |
2.1 | General Features | 24 |
2.2 | Deformed Bands | 27 |
2.3 | Transformed Bands | 28 |
2.4 | Variables Relevant to Adiabatic Shear Banding | 35 |
2.5 | Adiabatic Shear Bands in Non-Metals | 44 |
3 | Fracture and Damage Related to Adiabatic Shear Bands | 54 |
3.1 | Adiabatic Shear Band Induced Fracture | 54 |
3.2 | Microscopic Damage in Adiabatic Shear Bands | 57 |
3.3 | Metallurgical Implications | 69 |
3.4 | Effects of Stress State | 73 |
4 | Testing Methods | 76 |
4.1 | General Requirements and Remarks | 76 |
4.2 | Dynamic Torsion Tests | 80 |
4.3 | Dynamic Compression Tests | 91 |
4.4 | Contained Cylinder Tests | 95 |
4.5 | Transient Measurements | 98 |
5 | Constitutive Equations | 104 |
5.1 | Effect of Strain Rate on Stress-Strain Behaviour | 104 |
5.2 | Strain-Rate History Effects | 110 |
5.3 | Effect of Temperature on Stress-Strain Behaviour | 114 |
5.4 | Constitutive Equations for Non-Metals | 124 |
6 | Occurrence of Adiabatic Shear Bands | 125 |
6.1 | Empirical Criteria | 125 |
6.2 | One-Dimensional Equations and Linear Instability Analysis | 134 |
6.3 | Localization Analysis | 140 |
6.4 | Experimental Verification | 146 |
7 | Formation and Evolution of Shear Bands | 155 |
7.1 | Post-Instability Phenomena | 156 |
7.2 | Scaling and Approximations | 162 |
7.3 | Wave Trapping and Viscous Dissipation | 167 |
7.4 | The Intermediate Stage and the Formation of Adiabatic Shear Bands | 171 |
7.5 | Late Stage Behaviour and Post-Mortem Morphology | 179 |
7.6 | Adiabatic Shear Bands in Multi-Dimensional Stress States | 187 |
8 | Numerical Studies of Adiabatic Shear Bands | 194 |
8.1 | Objects, Problems and Techniques Involved in Numerical Simulations | 194 |
8.2 | One-Dimensional Simulation of Adiabatic Shear Banding | 199 |
8.3 | Simulation with Adaptive Finite Element Methods | 213 |
8.4 | Adiabatic Shear Bands in the Plane Strain Stress State | 218 |
9 | Selected Topics in Impact Dynamics | 229 |
9.1 | Planar Impact | 230 |
9.2 | Fragmentation | 237 |
9.3 | Penetration | 244 |
9.4 | Erosion | 255 |
9.5 | Ignition of Explosives | 261 |
9.6 | Explosive Welding | 268 |
10 | Selected Topics in Metalworking | 273 |
10.1 | Classification of Processes | 273 |
10.2 | Upsetting | 276 |
10.3 | Metalcutting | 286 |
10.4 | Blanking | 293 |
Appendices | 297 | |
A | Quick Reference | 298 |
B | Specific Heat and Thermal Conductivity | 301 |
C | Thermal Softening and Related Temperature Dependence | 312 |
D | Materials Showing Adiabatic Shear Bands | 335 |
E | Specification of Selected Materials Showing Adiabatic Shear Bands | 341 |
F | Conversion Factors | 357 |
References | 358 | |
Author Index | 369 | |
Subject Index | 375 |
Resumo:
Recently, the size dependence of mechanical behaviors, particularly the yield strength and plastic deformation mode, of bulk metallic glasses (BMG) has created a great deal of interest. Contradicting conclusions have been drawn by different research groups, based on various experiments on different BMG systems. Based on in situ compression transmission electron microscopy (TEM) experiments on Zr41Ti14Cu12.5Ni10Be22.5 (Vit 1) nanopillars, this paper provides strong evidence that shear banding still prevails at specimen length scales as small as 150 nm in diameter. This is supported by in situ and ex situ images of shear bands, and by the carefully recorded displacement bursts under load control its well as load drops under displacement control. Finite element modeling of the stress state within the pillar shows that the unavoidable geometry constraints accompanying such experiments impart a strong effect on the experimental results, including non-uniform stress distributions and high level hydrostatic pressures. The seemingly improved compressive ductility is believed to be due to such geometry constraints. Observations underscore the notion that the mechanical behavior of metallic glasses, including strength and plastic deformation mode, is size independent at least in Vit 1. (C) 2009 Acta Materialia Inc. Published by Elsevier Ltd. All rights reserved.
Resumo:
The tension and compression of single-crystalline silicon nanowires (SiNWs) with different cross-sectional shapes are studied systematically using molecular dynamics simulation. The shape effects on the yield stresses are characterized. For the same surface to volume ratio, the circular cross-sectional SiNWs are stronger than the square cross-sectional ones under tensile loading, but reverse happens in compressive loading. With the atoms colored by least-squares atomic local shear strain, the deformation processes reveal that the failure modes of incipient yielding are dependent on the loading directions. The SiNWs under tensile loading slip in {111} surfaces, while the compressive loading leads the SiNWs to slip in the {110} surfaces. The present results are expected to contribute to the design of the silicon devices in nanosystems.